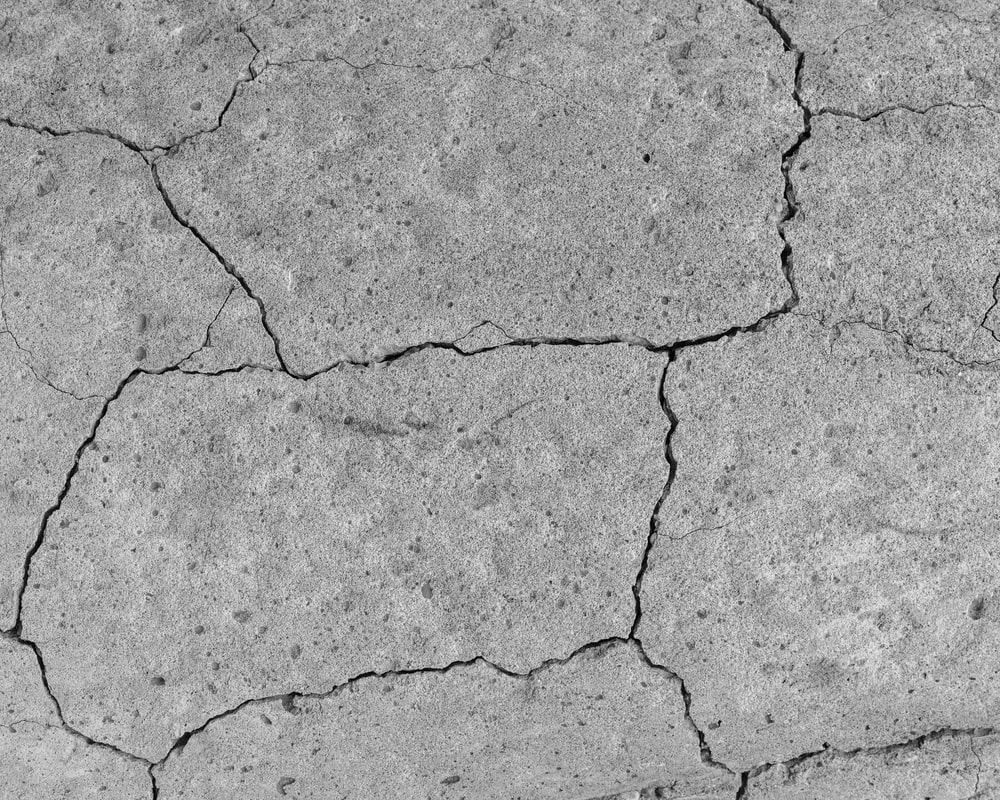
Cracked and crumbling concrete can compromise the aesthetics and safety of your residence. The deterioration process begins the moment it’s exposed to the elements.
Without proper maintenance, your concrete surfaces are left vulnerable to moisture, stains, and freeze-thaw cycles. Even high-quality installations cannot escape the ravages of time or weather.
However, with disciplined stewardship, a robust maintenance strategy can arrest decay, enlarging the functional longevity of your sidewalks, patios, and driveways. Regular, proactive care is the linchpin to preserving your concrete’s structural integrity and appearance.
Routine Concrete Cleaning
Periodic cleansing eliminates contaminants that can instigate concrete deterioration. Utilizing a pressure washer, with appropriate psi (pounds per square inch) settings, eradicates dirt without causing surface harm, when applied correctly. Such rigorous cleaning, ideally conducted biannually, can forestall the insidious encroachment of mold and mildew, preserving both aesthetics and material integrity.
Avoid caustic chemicals which might compromise your concrete’s constitution. Gentle, pH-neutral cleaners often yield sufficient results, ensuring the concrete remains unscathed while upholding its visual appeal and extending its lifespan.
Gentle Washing Techniques
Preserving your concrete’s integrity begins with gentle washing, using mild pH-neutral detergents that won’t harm the delicate surface layers. Opt for a soft-bristle brush to dislodge any dirt or debris softly.
Steer clear of harsh chemical cleaners and instead utilize a diluted vinegar solution, offering a natural and mild alternative. Apply this mixture with a spray bottle and allow it to sit before scrubbing gently for optimal results.
Concrete longevity can be significantly upheld through regular, gentle cleaning routines.
When rinsing, employ low-pressure water to prevent surface etching and to conserve water. A systematic approach ensures every area is covered without excessive water pressure that can damage the concrete. After washing, allow the surface to dry fully, ensuring moisture doesn’t linger to potentially damage the structure.
Stain Removal Essentials
Timely removal of stains is critical to maintain the aesthetic and integrity of concrete surfaces.
- Promptly treat spills to prevent the substance from penetrating deeper into the concrete.
- Identify the stain type as treatment varies—organic, inorganic, or oil-based each require specific approaches.
- Use degreasers for oil stains, applying them according to the manufacturer’s instructions for optimal results.
- Employ pH-neutral cleaners for general stains, and consider specialized products for tougher stains.
- Rinse thoroughly after cleaning to remove any residual cleaning agents.
It’s essential to use appropriate cleaning agents for different types of stains, even if the concrete cleaner is eco-friendly.
Frequent and correct cleaning methods prolong the life and appearance of your concrete.
Sealant Application Strategies
Applying a high-quality sealant is pivotal in safeguarding your concrete surfaces from moisture intrusion, chemical degradation, and climatic stresses. For effectiveness, choose the right sealant type—silicate, silicone, or acrylic-based—matching the specific needs of the concrete environment. Clean and dry the surface thoroughly before application, avoiding application in extreme temperatures which can compromise the seal. Employ methodical techniques, utilizing a roller or sprayer for uniform coverage, and ensure edge-to-edge application to seal the entire surface. Multiple, thinner coats are preferable to a single, thick layer, promoting better absorption and adhesion for long-term protection. Regular resealing, typically every 2-5 years, is essential to maintain an impenetrable moisture barrier and extend the lifespan of the concrete.
Choosing the Right Sealant
Selecting an appropriate sealant is a critical decision, pivotal to the longevity and durability of concrete surfaces.
The type of sealant must align with the concrete’s environmental exposure and intended use. Acrylics are suitable for mild climates and light traffic areas, penetrating sealers protect against moisture and chlorides for drivable surfaces, while epoxy or urethane sealants offer enhanced resistance for industrial settings. Each category has its distinct application protocols and longevity, hence detailed product comparison is indispensable.
Additionally, consider the sealant’s compatibility with your concrete’s specific characteristics. Sealants vary in terms of their ability to bond with different concrete finishes and textures. Therefore, it is prudent to consult a professional or refer to manufacturer guidelines to ascertain the optimal product for your concrete’s composition and surface condition.
Finally, ecological and safety considerations must not be overlooked when choosing a sealant. Opt for products with low volatile organic compound (VOC) emissions to ensure a safer environment during and after application. High-quality, environmentally-friendly sealants not only provide robust protection but also contribute to a healthier living space. Be aware that these factors together with the right application method play a substantial role in the efficacy and sustainability of the sealant over the lifespan of the concrete.
Sealant Application Process
Before initiating the application, the concrete surface must be thoroughly cleaned to remove dirt, stains, and existing sealants or finishes. This ensures optimal adherence of the new sealant to the concrete surface.
Next, select the appropriate type of sealant for your specific concrete needs. A penetrating sealer will infiltrate the surface to create a protective barrier, while a film-forming sealant will sit atop the concrete, offering a lustrous finish. Always check the manufacturer’s instructions for the recommended application method and conditions, including temperature and humidity levels, to ensure the sealant adheres correctly and cures without issues.
Importantly, when applying sealant, uniform coverage is crucial. Use a sprayer, roller, or brush designed for sealant application, working in sections to maintain a wet edge and prevent overlap marks. Allow the sealer to penetrate the surface, but be vigilant to avoid puddling, which can lead to an uneven coating and improper curing.
To conclude the process, ensure adequate drying time as specified by the sealant manufacturer. It is essential to limit foot traffic and keep the surface dry during this period to prevent any imperfections from forming. Maintaining this vigilance ensures that the sealant offers maximum protection, extends the life of your concrete, and enhances its appearance, ultimately safeguarding your investment for the years to come.
Crack Management
Proactive attention to cracks is paramount in the maintenance of concrete. When initial fissures appear, swift intervention prevents moisture intrusion, which can exacerbate the damage. Sealing cracks promptly can stave off further deterioration, ensuring the structure’s integrity and prolonging its service life.
In the realm of crack management, think of cracks as the initial sign of concrete distress. Address them using a methodical approach, employing a suitable crack filler that adheres to the concrete and can accommodate its movement. Remember, cracks are more than cosmetic blemishes—they can be precursors to significant structural issues if not promptly and effectively addressed.
Early Detection Tactics
Early detection of concrete deterioration is crucial. Promptly identifying changes, such as color shifts, cracking, or spalling, can prevent extensive and costly damage. Consistent visual inspections and a proactive approach to maintenance are instrumental in safeguarding the material’s integrity.
Regular surveillance of concrete surfaces is key to early detection. Look for subtle cues that suggest weakening or wear.
In particular, monitoring high-traffic areas where the concrete is subject to continuous stress will reveal early signs of degradation.
Changes in texture, such as flaking or pitting, are indicative of concrete distress and should be addressed immediately.
Incorporate a schedule of routine evaluations into your property’s maintenance plan, emphasizing the importance of identifying and addressing hairline fractures before they can evolve into wider, more problematic cracks.
Finally, leveraging technologies such as moisture meters or penetrant testing can uncover underlying issues not visible to the naked eye. Adopting these methods early in your maintenance routine enhances the likelihood of intercepting problems before they accelerate.
Effective Crack Repair Methods
Prior to initiating repairs, an accurate assessment of the crack’s breadth and depth is critical.
For narrow, non-structural cracks, the application of a concrete-specific sealant can be an efficient solution. Such sealants are tailored to flex with the concrete, creating a durable bond that mitigates water entry and further degradation. These sealants often contain polyurethane or epoxy compounds, providing strong adhesion and resistance to weathering. It’s essential to carefully follow the manufacturer’s instructions for proper application and curing times.
When addressing wider cracks or those that compromise structural integrity, a methodical approach is essential. This often involves chiseling out the crack to create a uniform space, then filling it with a concrete patching compound. Once filled, the area should be smoothed to align with the surrounding surface and allowed to cure fully, which stabilizes the repair and prevents further damage.
For large-scale or complex concrete repair projects, enlisting the services of a professional may be prudent. They will have access to advanced materials and methods, like epoxy injection or routing and sealing, which are not typically practical for DIY application. Comprehensive strategies like these not only rectify the visible issues but also work at consolidating the concrete’s structure, thereby restoring its original strength and prolonging its lifespan.
Preventive Measures and Practices
To preempt deterioration, engage in regular inspection of your concrete surfaces, diligently looking for signs of wear such as small cracks or divots. Prompt attention to these minor blemishes can halt the progression of damage, fortifying your concrete against the invasive elements that exacerbate such defects. Establishing a routine cleaning regimen also plays a vital role, as it eradicates harmful substances that may lead to degradation over time.
Integrating concrete sealants into your maintenance protocol is akin to applying a protective shield. These specially formulated products repel water, oil, and other contaminants, thereby diminishing the penetration of materials that induce deterioration. It is important to select a sealant that harmonizes with the type of concrete and the specific environmental conditions it faces. Moreover, applying the sealant as directed, which typically involves thorough preparation of the surface and careful adherence to the designated drying times, ensures the protective barrier functions optimally.
Environmental Damage Control
To withstand harsh environmental elements, apply surface treatments that buffer against freeze-thaw cycles and chemical deicers. These substances catalyze concrete spalls and cracks, compromising stability and aesthetics.
Employ quality sealers designed for extreme weather. Such products protect against moisture ingress, which can cause substantial damage over time.
Note that excessive sunlight and high temperatures may lead to concrete expansion, resulting in superficial or structural fissures. Tracking the environmental conditions enables proactive adaptation of maintenance procedures, ensuring a resilient response to climatic fluctuations.
Conclusively, ensure that run-off control measures are in place. Effective water management minimizes the risk of erosion and sedimentation build-up adjacent to concrete structures. Implementing adequate drainage systems and maintaining nearby vegetation can bolster your property’s defenses against water-related damage, playing a crucial role in environmental damage mitigation. Regular evaluation of these systems ensures they continue to perform their essential functions effectively.
Scheduled Maintenance Planning
Establish a regular maintenance schedule to preserve concrete integrity. Frequent inspections ensure issues are addressed promptly, forestalling extensive deterioration.
Incorporate routine cleaning as a foundational practice. Dust and debris removal prevents surface abrasion and staining.
Consider seasonal checks to anticipate and remedy challenges posed by weather. For instance, arranging for sealant application before winter can avert freeze-thaw damage that can be detrimentally impactful to concrete surfaces.
Structured upkeep plans can significantly delay the need for large-scale repairs, which can be costly and disruptive. Maintenance activities such as sealing, cleaning, and minor repair work should be calendared to align with the climatic conditions that exert the greatest stress on concrete structures. This prescient approach can stave off costly repairs and maintain structural integrity for years to come.
Rely on Cincinnati Custom Concrete for exceptional concrete contracting in Cincinnati, OH.